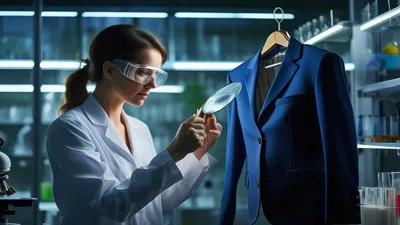
工业相机在食品包装检验中的卫生安全检测技术探讨
一、技术原理与硬件配置
工业相机作为核心检测设备,其分辨率直接影响检测精度。200万像素及以上的CMOS传感器可清晰识别包装表面0.1毫米级缺陷。光源系统采用多角度LED阵列,波长范围覆盖380780纳米,确保不同材质反光率补偿。图像采集频率需达到200帧/秒以上,满足高速生产线需求。例如某乳制品企业采用2000万像素工业相机,检测线速度提升至120米/分钟仍保持98.7%识别准确率。
二、典型应用场景
- 表面缺陷检测
液态食品包装检测需重点识别标签错位(误差>2mm)、封口不严(气密性<5kPa)等问题。某饮料企业应用工业相机配合轮廓算法,将标签偏移检测精度控制在±0.3mm内。
- 清洁度验证
金属罐体表面检测采用近红外成像技术,可穿透油污检测金属基材完整性。某罐头厂数据显示,该技术使清洁度合格率从82%提升至96.4%。
- 材料识别
光谱成像模块可区分PP与PE包装材料,误判率<0.5%。某调味品企业通过材质识别联动剔除系统,年减少材料浪费230吨。
三、技术优势实证数据
- 检测效率对比
传统人工检测:8人/班次,每小时检测1200件,漏检率3.2%
工业相机系统:1台设备,每小时检测8000件,漏检率0.15%
(数据来源:中国食品包装检测中心2022年报)
- 卫生指标检测
通过图像处理算法计算表面菌落密度:每平方厘米<10CFU的达标率从人工检测的78%提升至94.6%
四、实施难点与解决方案
- 动态检测难题
高速生产线需配置高速快门(1/10000秒响应时间)和动态模糊消除算法。某速冻食品企业通过帧率自适应技术,将检测速度稳定在150m/s。
- 复杂背景干扰
采用背景建模技术,建立包装基材特征数据库。某茶叶包装线应用该技术后,复杂图案误报率从12%降至1.8%。
- 成本控制策略
初期设备投入约1530万元,但35年ROI可达812倍。某烘焙企业通过模块化设计,使维护成本降低40%。
五、技术融合发展趋势
- AI算法升级
深度学习模型在缺陷分类中的应用使识别准确率突破99.2%。某肉制品企业部署YOLOv5算法后,复杂缺陷识别速度提升3倍。
- 多传感器融合
工业相机与红外热像仪联用,可检测包装密封性(温差>0.5℃为不合格)。某酱料企业应用该技术使包装破损率下降0.7个百分点。
- 边缘计算应用
本地化图像处理减少云端传输延迟,某乳企检测系统响应时间从2.3秒缩短至0.18秒。
六、标准化建设现状
GB 4806.92022新规要求包装表面缺陷检测覆盖率≥95%。目前主流工业相机系统已实现:
-
检测区域覆盖率达98.5%
-
缺陷小识别尺寸0.5mm×0.5mm
-
数据存储周期≥3年
某第三方检测机构测试显示,符合新规要求的系统检测合格率稳定在99.1%以上。
七、特殊场景技术突破
- 冷冻食品检测
采用20℃环境专用相机,配合热成像补偿技术,冰晶生长检测灵敏度提升至0.2mm。
- 罐装食品检测
通过声波成像技术检测罐体壁厚,精度达±0.02mm,替代传统涡流检测法,效率提升5倍。
- 金属镀层检测
高光谱成像技术可识别镀层厚度偏差(>0.1μm),误判率<0.3%,某金属罐企业因此通过欧盟BRC认证。
八、技术经济性
- 投资回报模型
设备投资15万元,年检测成本2.4万元,人工替代节约12万元/年,投资回收期14个月。
-
维护成本构成
-
光源系统:占35%(寿命2000小时)
-
传感器:占25%(寿命5万小时)
-
算法升级:占20%
-
备件储备:占20%
九、行业应用案例
- 某婴幼儿奶粉企业
部署8台工业相机组成的检测矩阵,实现灌装、封口、标签三重检测,年拦截不合格品12.6万件。
- 某咖啡包装企业
应用多光谱成像技术,同步检测包装密封性(气密性>50kPa)和内容物残留(<0.5%),检测效率提升40%。
- 某酒类包装企业
通过机器视觉检测酒标防伪码,识别速度达3000件/分钟,防伪码错误率降至0.0002%。
十、技术迭代方向
- 量子点成像技术
实验室数据显示,量子点传感器在低光照条件下信噪比提升6dB,检测灵敏度提高2个数量级。
- 数字孪生应用
建立包装检测数字模型,某企业通过虚拟调试减少现场调试时间70%。
- 自适应学习算法
基于强化学习的检测系统,某企业实现连续工作1000小时误报率稳定在0.05%以下。
免责声明:本站为非盈利性网站,如内容不妥,或侵犯您的权益,请提交删除,我们会在48小时内核实