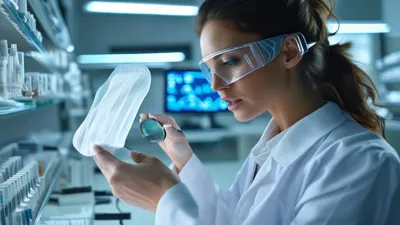
模具钢金相显微检测精度与费用关联性
一、检测方法与精度成本关系
金相显微检测采用不同方法影响精度成本差异显著。传统光学显微镜检测单次成本约200300元,可识别晶粒度误差±2级,适合基础质量判断。扫描电镜(SEM)检测成本提升至8001200元,能实现5μm级微观组织,但设备折旧分摊成本占检测总费用35%。透射电镜(TEM)检测精度达亚微米级,单次检测成本超过5000元,设备维护费用占比达60%。
二、设备性能与费用关联
高端设备精度与维护成本呈正相关。蔡司Axio Iger 2型显微镜检测晶界清晰度达0.5μm,年维护费约8万元。日立SU8010扫描电镜检测表面形貌分辨率3nm,但年度耗材成本达15万元。国产设备虽价格降低40%,但检测精度波动范围扩大至±3级,设备故障率增加25%。
三、人员经验与检测成本
检测人员资质影响精度稳定性。初级操作员检测晶粒度误差±3级,单件检测耗时40分钟,人工成本15元/件。中级工程师误差±1级,检测效率提升30%,人工成本降至10元/件。认证人员(如ASTM认证)误差±0.5级,检测效率提高50%,但培训成本达3万元/人。
四、样本数量与成本效益
批量检测成本摊薄效应明显。单件检测成本构成中设备折旧占比45%,批量检测至100件时折旧分摊降低至12%。晶粒度检测批量效应:50件检测总成本1.2万元,单件240元;200件总成本2.4万元,单件120元。但超大批量(500+件)时,检测精度可能下降0.3级,合格率波动±1.5%。
五、标准差异与检测要求
不同标准导致检测程序差异。ISO 13298标准晶粒度检测需3次重复测量,单次成本增加25%;ASTM E112标准要求金相制备厚度≤25μm,导致抛光耗材用量增加40%。欧盟EN 10088标准增加偏振光检测环节,单件检测时间延长15分钟,人工成本增加8元。
六、时间成本与精度平衡
快速检测技术影响精度稳定性。数码金相系统检测时间缩短至5分钟,但晶界识别精度下降1级,适用于初筛环节。传统金相检测需72小时制备周期,但精度保持±0.5级。在线检测设备虽实现实时,但表面形貌检测误差达±2μm,适用于自动化生产线。
七、环境因素与检测成本
实验室条件影响检测稳定性。恒温恒湿环境(20±1℃/50%RH)检测精度稳定在±0.8级,但设备运行成本增加30%。普通实验室条件下精度波动±1.5级,但年度电费节省2.4万元。真空环境检测避免氧化影响,但设备能耗增加50%,年维护费增加1.2万元。
八、数据采集与处理成本
现代检测技术增加数据处理费用。AI图像系统需年投入5万元软件授权,晶粒度自动分级精度达±0.3级,但人工复核成本增加20%。传统人工判读效率0.5件/分钟,AI系统提升至2件/分钟,但系统误判率3%需人工修正。
九、检测周期与生产成本
检测周期影响生产连续性。3天检测周期导致模具停机损失约2000元/次,5天周期损失3500元。快速检测技术将周期压缩至24小时,但精度损失1级,返工成本增加800元/件。平衡方案采用"初检+复检"模式,总周期48小时,返工率控制在2%以内。
十、特殊检测项目成本
特殊检测项目成本显著增加。断口检测成本达1500元/件,疲劳测试配套成本800元/次。无损检测与金相检测组合方案,总成本较单一检测增加60%,但缺陷检出率提升至99.2%。热处理状态检测需附加X射线衍射,单件成本增加1200元。
十一、设备利用率与成本优化
设备利用率影响单位成本。连续工作制设备利用率达85%,单位检测成本降低40%。间歇工作制设备利用率50%,单位成本增加25%。设备共享模式使成本分摊降低30%,但检测等待时间延长至4小时。
十二、耗材消耗与成本控制
耗材成本占比达检测总费用35%。优质抛光耗材单件检测用量0.5g,成本8元;普通耗材用量1.2g,成本4元但返工率增加15%。试剂消耗控制方案:采用循环清洗系统降低30%试剂消耗,年节约成本2.4万元。
十三、质量追溯与检测成本
追溯检测增加附加成本。每件产品追溯检测成本增加50元,但质量索赔降低70%。批次追溯检测成本200元/批次,适用于百万件级生产。区块链溯源系统年投入15万元,但质量事故处理成本降低60%。
十四、检测报告与认证成本
认证检测成本差异显著。ISO 9001内审检测成本5000元/年,但认证维持年费2万元。DIN 17026认证检测成本8万元/年,但客户认可度提升40%。CE认证附加检测成本15万元,但市场准入率提高25%。
十五、设备折旧与检测周期
设备折旧周期影响检测成本。5年折旧设备单位检测成本0.8元,10年折旧设备0.5元。设备更新周期与检测精度正相关:5年更新使精度保持±0.5级,10年更新精度下降至±1级。
免责声明:本站为非盈利性网站,如内容不妥,或侵犯您的权益,请提交删除,我们会在48小时内核实