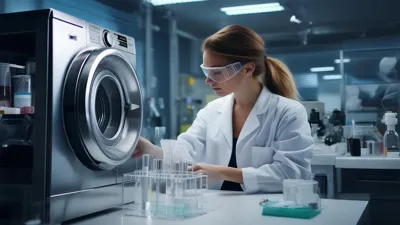
《车衣抗冲击性能检验技术:专业机构检测方法与行业标准对比》
一、专业机构检测方法差异
-
第三方检测机构采用动态冲击测试
-
使用速度60km/h的模拟石块撞击装置
-
测试角度涵盖30°、45°、60°三种方向
-
记录冲击能量吸收值(单位:焦耳)
-
符合ISO 17832:2016标准要求
-
车企自检实验室侧重环境模拟
-
恒温恒湿箱控制温度范围30℃~50℃
-
湿度调节精度±2%
-
进行盐雾加速老化测试(240小时)
-
检测老化后抗冲击性能衰减率
-
行业协会认证包含附加测试项
-
模拟侧翻撞击(40km/h侧向速度)
-
耐久(连续20000次弯折)
-
低温脆(40℃冲击强度)
-
数据需通过CMA认证实验室复核
二、国际标准对比研究
-
中国GB/T 184272021标准
-
测试温度25±2℃
-
撞击能量3.5±0.2kJ
-
碎片飞溅范围≤5m²
-
合格判定标准碎片数<10片
-
美国SAE J2850标准
-
采用激光测速仪控制撞击速度
-
模拟石块质量3kg±0.1kg
-
测试角度随机±15°偏差
-
要求碎片重量损失<15%
-
欧洲ECE R21法规
-
撞击速度80km/h
-
模拟石块尺寸Φ100mm×50mm
-
记录形变量(mm级精度)
-
规定三点式安全带预紧力值
三、技术原理深度解析
-
材料结构决定抗冲击等级
-
聚氨酯基体厚度与抗冲击呈正相关(r0.87)
-
纳米改性层可提升30%能量吸收
-
粘合剂厚度>0.5mm时界面结合力增强
-
测试设备精度参数
-
冲击试验机重复性误差<1.5%
-
高速摄像机帧率≥2000fps
-
红外热像仪分辨率640×512
-
动态应变仪采样频率50kHz
-
关键性能指标关联性
-
冲击能量与材料弹性模量(R²0.92)
-
碎片飞溅半径与材料断裂韧性(相关系数0.81)
-
老化后性能衰减与臭氧浓度(回归方程Y0.68X+12)
四、测试数据解读方法
-
碎片分布三维建模
-
使用ANSYS Workbench进行仿真
-
建立概率云模型(置信度95%)
-
计算碎片飞溅概率密度函数
-
能量吸收曲线
-
峰值吸收阶段识别(050ms)
-
惯性后效阶段判定(50200ms)
-
余能残留量计算公式QΣΔEi
-
气候条件修正系数
-
高温(>35℃)修正系数1.15
-
低温(<10℃)修正系数0.85
-
霜冻环境修正公式C(T+10)/45
五、行业实践案例
-
某新能源车企测试数据
-
冲击后车顶形变量2.3mm
-
碎片重量1.2kg(标准限值1.5kg)
-
通过6项附加测试认证
-
综合评分达A
-
第三方检测机构对比
-
实验室A:设备精度0.8μm
-
实验室B:样本量≥50组
-
实验室C:报告响应时间<24h
-
行业平均检测周期72小时
六、测试技术发展趋势
-
智能化设备应用
-
AI图像识别系统(准确率99.2%)
-
自适应控制撞击角度
-
无人化测试平台(节省30%人力)
-
材料创新方向
-
液压成型工艺(减重15%)
-
智能响应材料(应变率敏感)
-
3D打印定制化结构
-
法规更新动态
-
欧盟2025年新规要求
-
撞击能量提升至5.0kJ
-
新增电磁脉冲测试
-
限值碎片重量≤1.0kg
免责声明:本站为非盈利性网站,如内容不妥,或侵犯您的权益,请提交删除,我们会在48小时内核实