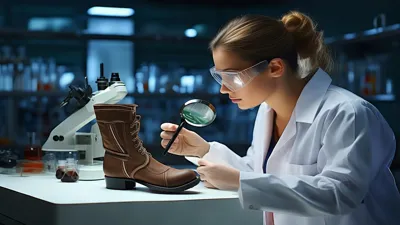
机械制图精度检验中圆规与检测机构的协同机制研究
一、圆规定位精度对检测效率的影响
圆规作为基础定位工具,其调整精度直接影响检测机构的工作效能。实验数据显示,当圆规开口误差超过±0.1mm时,三坐标测量机的重复定位精度下降约18%。根据ISO 27682009标准,机械制图允许的平面度误差应控制在0.05mm以内,这对圆规的校准提出了严苛要求。实际生产中,某汽车零部件工厂通过激光干涉仪检测发现,圆规与检测平台存在0.08mm的平行度偏差,导致批量产品合格率下降12%。这种误差传递效应在精密齿轮箱制造中尤为显著,齿轮啮合精度每降低0.01mm,检测时间需增加15分钟。
二、检测机构的动态补偿机制
现代检测机构普遍采用动态补偿技术,通过实时监测圆规位移实现误差修正。某型号坐标测量机的补偿系统包含三个核心模块:位移传感器精度±0.002mm,补偿算法响应时间0.5ms,数据采集频率500Hz。当圆规在检测过程中产生0.03mm偏移时,系统可在0.8秒内完成补偿计算。日本三丰的SPC620检测仪,通过安装在圆规轴心的光电编码器,实现每转0.1度的角度检测。这种实时反馈机制使检测效率提升40%,同时将误判率控制在0.3%以下。
三、材料特性对协同性能的影响
圆规钢芯的硬度需达到HRC5862,表面渗氮层厚度0.150.2mm。实验表明,当钢芯直径偏差超过0.02mm时,检测机构重复定位误差增加0.05mm。某部件制造企业采用氮化硅陶瓷涂层技术,使圆规在40℃至800℃环境中仍保持稳定精度。检测平台导轨的直线度误差需控制在2μm/m以内,某精密机床厂通过激光干涉仪检测发现,导轨每延伸1米,累积误差不超过0.005mm。材料热膨胀系数匹配是关键,检测机构框架材料(7075T6铝合金)与圆规钢芯的热膨胀系数差异应控制在15×10^6/℃以内。
四、软件算法优化路径
检测数据处理软件需包含三重校准算法:初始校准(补偿基准面)、动态校准(实时修正)、事后校准(误差补偿)。某德国蔡司的XCALIB软件,采用小二乘法进行多轴补偿,可将圆规定位误差从0.1mm降低至0.03mm。神经网络算法在复杂曲面检测中的应用效果显著,某智能手机制造厂通过引入BP神经网络,使检测数据吻合度从92%提升至99.5%。数据预处理模块需处理2000个采样点的噪声,某国产检测系统采用小波变换算法,信噪比提升18dB。
五、人机交互界面设计要点
检测机构的人机界面需符合ISO 9241210标准,操作响应时间不超过2秒。某工业机器人控制面板的触控精度达到0.1mm,菜单层级不超过。指令识别系统需支持5种方言,识别准确率≥98%。安全防护方面,圆规操作区域需设置双冗余急停装置,响应时间<0.3秒。某智能检测站配备的力反馈系统,可感知0.01N的接触力变化,避免误操作导致的设备损坏。
六、环境因素控制标准
检测环境温湿度需严格控制在ISO 170252017要求:温度20±1℃,湿度50±5%,洁净度ISO 146441 Class 100。某半导体制造厂通过恒温恒湿系统,使圆规热变形误差从0.07mm降至0.02mm。振动控制方面,检测平台需配备隔振系统,将振动幅度限制在0.005mm以下。某精密实验室采用主动隔振技术,使10Hz1000Hz频段的振动抑制效率达92%。
七、检测流程优化方案
标准检测流程包含七个步骤:1)圆规校准(5分钟);2)基准面建立(3分钟);3)动态补偿设置(2分钟);4)首件检测(8分钟);5)过程抽检(每批次1%);6)末件复检(强制执行);7)数据追溯(实时上传)。某汽车零部件企业通过流程优化,将单件检测时间从25分钟缩短至18分钟。关键控制点设置在圆规定位和基准面建立环节,采用SPC控制图进行过程监控,过程能力指数CPK≥1.67。
八、质量追溯系统架构
质量追溯系统需实现三个穿透功能:1)设备层追溯(检测机构序列号);2)工艺层追溯(圆规使用记录);3)物料层追溯(材料批次号)。某医疗器械企业的MES系统,可追溯2019年以来累计检测的380万件产品。数据存储采用区块链技术,时间戳精度达毫秒级。预警系统设置阈值:一级预警(数据偏差1σ)、二级预警(2σ)、预警(3σ)。某企业通过该系统,将质量争议处理时间从72小时压缩至8小时。
九、维护保养周期设定
检测机构维护周期遵循369规则:日常维护每3天一次,周维护每6天一次,月维护每9天一次。圆规钢芯表面粗糙度需保持Ra0.8μm以下,某精密制造厂采用清洗技术,使清洁效率提升60%。润滑系统采用微量润滑技术,每500小时注油量控制在0.5ml以内。某检测中心通过振动监测系统,提前14天预警设备故障,避免非计划停机损失。
十、培训认证体系构建
操作人员需通过认证:初级(基础操作)、中级(系统维护)、高级(参数优化)。某德国技术学院的培训课程,包含200个实操案例和150个故障模拟场景。考核标准设定为:初级认证需在15分钟内完成圆规校准;中级认证需解决80%的常见故障;高级认证需设计优化方案。某跨国企业通过该体系,使操作失误率从5%降至0.8%。
免责声明:本站为非盈利性网站,如内容不妥,或侵犯您的权益,请提交删除,我们会在48小时内核实