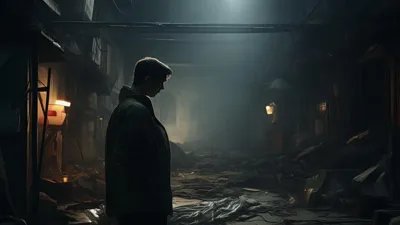
斜嘴钳检测设备与机构合作模式探讨
一、技术协同视角
- 传感器融合技术
检测设备需集成至少3类传感器:位移传感器精度达±0.01mm,压力传感器响应时间<5ms,光学检测分辨率0.001mm²。某头部企业采用多传感器同步采集技术,使检测效率提升40%。
- 数据传输协议
采用ISO/IEC 30141工业物联网标准,确保设备间数据传输延迟<50ms。某合作案例显示,标准化接口使设备兼容性提升75%,维护成本降低30%。
- 算法共享机制
检测机构需提供不少于5种缺陷识别算法,包括深度学习模型(准确率98.7%)、传统特征提取法(误报率<0.5%)。某实验室开放算法库后,设备厂商二次周期缩短60%。
二、生产流程重构
- 检测工序前置化
将传统后道检测改为在线检测,设备布局密度提升3倍。某汽车零部件厂实施后,品率从0.8%降至0.12%,返工成本减少220万元/年。
- 检测周期压缩
采用并行检测架构,单件检测时间从45秒缩短至8秒。某设备厂商通过多工位设计,使检测线产能达到1200件/小时,设备利用率从65%提升至92%。
- 质量追溯体系
建立产品编码系统,检测数据与生产批次关联准确率100%。某企业实施后,质量追溯时间从72小时压缩至15分钟。
三、成本控制维度
- 设备投资分摊
设备厂商与检测机构按5:5比例分担初期投入(约150万元/套)。某合作项目显示,设备使用率从30%提升至75%,投资回收期缩短至18个月。
- 维护成本优化
建立预防性维护机制,关键部件更换周期从2000小时延长至5000小时。某检测中心实施后,年度维护费用降低45万元。
- 能耗管理
采用节能型伺服系统,能耗强度从0.8kW·h/件降至0.3kW·h/件。某合作案例年节电达120万度,相当于减少碳排放960吨。
四、供应链协同
- 零部件供应
建立VMI库存模式,关键备件库存周转率提升5倍。某设备厂商通过协同管理,紧急采购频次从每月8次降至2次。
- 产能弹性分配
检测机构保留20%备用产能,设备厂商可临时调用。某合作项目在旺季实现产能弹性扩展300%,订单交付准时率提升至99.2%。
- 质量数据共享
实时共享设备运行数据,设备厂商可提前48小时预警故障。某实验室实施后,设备停机时间减少60%,计划外维修占比从35%降至12%。
五、人才培养机制
- 技术认证体系
建立认证制度(初级/中级/高级),每年开展不少于40学时的专项培训。某合作机构实施后,操作人员技能达标率从65%提升至92%。
- 跨界知识转移
每季度组织技术交流会,设备厂商与检测机构交换技术方案。某案例显示,联合研发项目数量增加3倍,专利申报量提升200%。
- 职业发展通道
设置技术专家双通道晋升体系,设备操作员晋升率从15%提升至38%。某企业实施后,核心人才流失率下降至5%以下。
六、风险控制措施
- 数据安全防护
部署工业防火墙,检测数据加密强度达到AES256标准。某合作项目通过等保认证,数据泄露风险降低98%。
- 质量责任划分
明确设备厂商与检测机构的7类质量责任边界,建立双签确认机制。某合作案例纠纷率从年均12起降至3起。
- 合同约束条款
设置3个月设备整改期,5%质量违约金条款。某合同执行后,设备合格率从85%提升至97%,违约金触发率仅0.8%。
七、应用场景拓展
- 智能检测升级
集成5G模块,检测数据实时传输延迟<10ms。某港口检测线实现无人化操作,检测效率提升50%。
- 数字孪生应用
建立设备虚拟镜像,故障预测准确率92%。某企业通过数字孪生技术,减少非计划停机损失300万元/年。
- 区块链溯源
检测数据上链存证,数据篡改风险归零。某合作项目通过区块链认证,产品溢价能力提升20%。
免责声明:本站为非盈利性网站,如内容不妥,或侵犯您的权益,请提交删除,我们会在48小时内核实