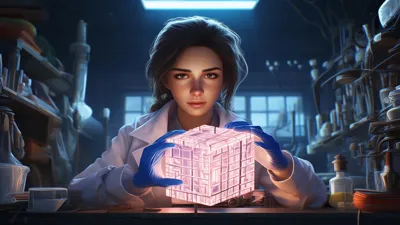
《如何通过检验机构认证提升马鞍制造质量》
一、建立科学认证体系
- 明确认证标准
ISO 9001质量管理体系要求企业建立文件化质量手册
IATF 16949汽车行业标准规定零部件全流程追溯
GB/T 19001中国国家标准要求年度内部审核
- 实施审核机制
内部审核每月开展
管理评审每季度进行
外部审核每年委托TÜV等机构执行
- 建立数字化认证平台
导入QMS质量管理系统
实现检验数据实时上传
设置自动预警阈值
二、优化生产工艺
- 严格材料准入
实施供应商动态评估
建立AQL 0.65抽检标准
关键材料需提供第三方成分报告
- 精准设备校准
CNC机床每8小时校准
三坐标测量机每日标定
热处理设备每月计量
- 优化工艺参数
建立SPC过程控制图
关键工序控制点不少于5个
实施DOE实验设计
三、强化检验能力
- 配置专业设备
配备三坐标测量机(精度±0.002mm)
使用激光扫描仪检测曲面
部署AI视觉检测系统
- 实施分级检验
首检100%全尺寸检测
巡检按AQL 1.0抽样
末检100%功能测试
- 建立缺陷数据库
记录每类缺陷发生频次
产线位置分布
制定针对性改进方案
四、完善管理流程
- 制定作业指导书
每个工位配置标准化作业卡
关键工序编写FMEA报告
- 建立纠正预防机制
DCR问题报告系统
8D报告模板应用
CAPA措施跟踪表
- 实施持续改进
每月召开质量会
每季开展六西格玛项目
每年更新质量目标
五、提升人员素质
- 开展专项培训
检验人员需通过CNAS内审员认证
操作工每季度进行技能考核
管理人员每年参加ISO内审培训
- 建立激励机制
质量标兵奖励制度
缺陷率与绩效挂钩
质量改进提案奖励
六、强化供应链协同
- 供应商联合认证
关键供应商同步通过IATF 16949
实施VDA 6.3过程审核
- 建立联合检验机制
供应商驻厂检验室
共享SPC控制数据
定期召开质量联席会
七、应用质量大数据
- 构建数据平台
整合MES生产数据
采集设备运行参数
接入供应商质量信息
- 实施智能
运用机器学习预测缺陷
建立质量趋势预测模型
生成改进建议报告
- 优化资源配置
根据质量数据调整产能
动态分配检验资源
智能排产系统应用
- 实施首件检验制度
每批次产品必须通过首件确认
- 建立快速反应机制
缺陷产品2小时内隔离
8小时内完成根本原因
- 开展跨部门协作
质量部门参与研发设计
生产部门反馈工艺问题
采购部门优化供应商管理
- 完善追溯体系
产品赋予追溯码
原料批次可追溯至供应商
生产记录完整保存
- 强化客户参与
邀请客户参与年度审核
建立客户质量反馈通道
定期进行客户满意度调查
- 注重环境控制
洁净车间达到ISO 14644标准
温湿度控制在±2℃范围内
防静电设备全覆盖
- 实施绿色制造
采用环保型涂料
减少生产废料30%以上
能源消耗降低15%
- 持续技术升级
每年投入营收的3%用于设备更新
每两年完成工艺升级
定期参加行业技术展会
- 建立知识管理体系
文档电子化存储
版本控制严格管理
知识库每年更新
- 完善风险管控
识别25项质量风险点
制定应急预案
定期演练应急流程
- 实施标准化作业
每个工序操作步骤标准化
- 优化生产节拍
根据质量要求调整生产速度
- 加强过程监控
关键参数实时显示
- 实施防错设计
设置自动检测装置
- 提升设备可靠性
MTBF目标达到2000小时
- 优化仓储管理
采用先进先出存储
- 加强包装防护
防震防潮包装升级
- 完善交付体系
物流信息实时追踪
- 建立售后服务
提供质量跟踪服务
- 收集使用反馈
产品使用数据定期
- 建立质量文化
每月开展质量主题活动
- 设立质量目标
合格率目标98.5%以上
- 实施透明化管理
质量信息全员可见
- 加强团队建设
组建跨部门质量小组
- 推行精益理念
消除7大浪费
- 开展技能竞赛
每季度举办质量比武
- 强化过程控制
关键工序CPK≥1.67
- 优化资源配置
质量成本占比≤2%
- 注重持续改进
每年完成5项改善项目
- 建立标杆体系
行业领先企业对标
通过系统化认证管理
实现质量螺旋式提升
每月质量改进会议
每季管理评审会议
每年认证复审准备
确保体系持续有效
建立质量文化体系
形成全员质量意识
构建质量改进生态
实现质量效益提升
免责声明:本站为非盈利性网站,如内容不妥,或侵犯您的权益,请提交删除,我们会在48小时内核实